Tag Archive: Zylinderkopf
14. Original Golf 1-Treffen in Wolfsburg 2012 – Rückblick
Ja, ich war gestern in Wolfsburg. Ja, es hat gestern geregnet. Damit wären diese beiden Fragen schon mal gleich vorneweg beantwortet.
Außerdem, geplant ist geplant. Da können uns auch so ein paar Regentropfen nicht von abhalten.
Von der 32er-Fraktion waren wieder Dirk, Michael und ich auf dem Platz. Hat sich ja schon seit Jahren so eingebürgert, daß wir uns hier treffen. (mehr …)
Nach dem Tausch der Ventilfedern kam die Ernüchterung
Es muß auf der Heimfahrt von der Rallye am letzten Wochenende passiert sein. Irgendwie habe ich beim Auffahren auf die Autobahn „vergessen“ rechtzeitig zu schalten. Die Nadel vom Drehzahlmesser befand sich am Ende der Skala. Seitdem gibt der Motor ein komisches Klappern von sich. Sonst ist ihm aber nichts anzumerken, Öldruck ist i.O. und er läuft auch noch völlig normal.
So habe ich dem auch erstmal keine weitere Bedeutung zugemessen. Ich habe mich zunächst den Ventilfedern gewidmet. Die wollte ich zur Sicherheit auf jeden Fall noch tauschen. Es kann ja passieren, daß ich des öfteren mal in Drehzahlregionen jenseits der 7200 Umdrehungen komme. Sicher ist sicher. Zumal auch der Ventilhub über das, von VW freigegeben Maß, hinausgeht.
Dazu mußte die Nockenwelle wieder raus.
Das ist bei den 827er-Motoren aber nicht weiter der Rede wert. Sieht alles noch richtig sauber aus. Hier sind auch keinerlei Gründe für das Klappern erkennbar.
Ölverlust beseitigt, Vergasercheck und den GLS gestartet
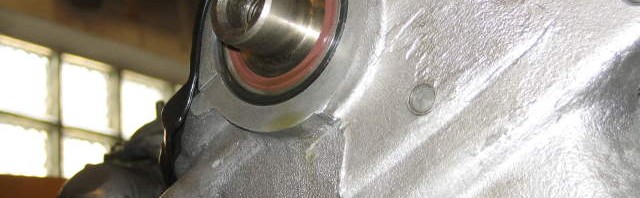
Gestern habe ich mich noch mal um ein paar Kleinigkeiten gekümmert, die bisher immer hinter wichtigeren Dingen zurückstehen mußten.
Zum einen war da der Ölverlust vorne am Zylinderkopf. Leider hat man durch das verstellbare Nockenwellenrad jetzt keinen direkten Durchblick mehr auf den Bereich.
Das Rad mußte also wieder runter und dann war die Sache auch gleich klar.
Eindeutiger gehts kaum. Der Nockenwellensimmering ist inkontinent. Vielleicht war ich beim Einbau etwas zu rabiat, vielleicht taugte der auch einfach nichts. An der Zwischenwelle habe ich die slebe Marke verbaut. Da gibts es bisher kein Problem.
Ist jetzt auch egal. Durch den alten Ring eine Blechschraube gejagt und ihn damit dann rausgeholt.
Den neuen habe ich dann mit dem alten Ring und einem alten Nockenwellenrad reingedrückt.
Nach dem Einbau habe ich den Motor kurz angeschmissen. Bisher siehts gut aus. Ich mußte aber wieder relativ schnell abstellen, da jetzt zwar Wasser drauf ist, aber die Lima noch daneben liegt. Der Keilriemen somit zwangsläufig auch.
Nächster Punkt waren die Kabel für für die Druck- und Temperaturanzeige vom Öl. Die lagen auch noch so halbfertig im Wasserkasten rum. Entlang des original Kabelbaums gings Richtung Kabeldurchführung in der Spritzwand.
Vom Motorraum aus schob ich die Kabel dann durch die Kabeldurchführung nebem dem Hauptbremszylinder. Zu meinem Glück lagen die Kabel danach schon griffbereit im Fußraum.
Innen gehts dann weiter wenn der Wagen von der Bühne ist und ich die Türen vernüftig aufmachen kann.
An der Kühlerpappe hatte sich beim Ausbau ein kleine Ecke verabschiedet. Die habe ich fachmännisch wieder an ihren Platz zurückgebracht.
Dann gings noch mal an den Vergaser hier wollte ich noch mal so einige Sachen checken, die für die die einwandfreie Funktion später wichtig sind.
Dazu gehörte die Prüfung der Pull-Down-Membrane und die dazugehörige Überprüfung des Starterklappenspalts.
Mittels Unterdruckpumpe die Membrane betätigt und das entsprehende Maß eingestellt. Der Sollwert lag bei genau 4,5 mm, sodaß ich einen normalen Bohrer als Lehre nehmen konnte.
Gut das mich noch mal um dem Vergaser gekümmert habe. Ich wäre wohl sonst mit ziemlich bedröppelten Gesicht von der ersten Probefahrt zurückgekommen.
Die Drosselklappe der zweiten Stufe ging nämlich überhaupt nicht auf. Die Membrane war in Ordnung, aber die Klappe war total verharzt. Die Kraft der Dose langte nicht um sie zu öffnen.
Mit etwas Rostlöser und mehrmaligen Betätigen per Hand ging sie hinterher wieder so leicht, daß sie auch mit der geringen Kraft des Unterdrucks nun wieder einwandfrei öffnet.
Da ist der letzte Besitzter dieses Vergaser wohl immer nur auf Sparflamme gefahren.
Die Einstellung der Startautomatik muß ich noch mal checken. Dafür war der Motor gestern aber nach dem kurzen Probelauf schon zu warm. Muß ich noch mal machen, wenn er vorher nicht gelaufen hat.
Damit war in der Werkstatt erstmal Feierabend. In der heimischen Garage gings dann aber noch mal kurz weiter. Falls heute wieder so schönes Wetter wird, will ich auf jeden Fall vorbereitet sein.
Also noch mal sehen ob der GLS nach der Winterpause anspringt. Natürlich nicht. Batterie war fast leer. Was nützt das beste Erhaltungsladegerät wenn man es nicht benutzt…..
So mußte ich doch wieder, das große Ladegerät mit der Starthilfefunktion anschließen. Nach dem üblichen georgel wegen fehlendem Sprit ist er dann aber einwandfrei angesprungen.
Mal sehen ob´s morgen eine kleine Tour gibt. Das Erhaltungsladegerät ist jetzt auf jeden Fall angeklemmt.
Wasser marsch!, Feuer frei! und Prost!
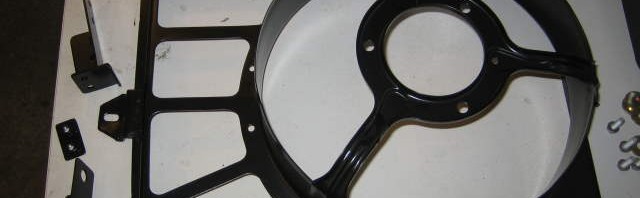
Gestern vormittag habe ich endlich meine langersehnte Lieferung erhalten. Das Lüfterblech für den Kühler und die Ölkühlerhalter sind zurück vom Pulverbeschichten.
Damit war meine zunächst angedachte Tagesplanung natürlich sowas von hinfällig. Alles andere abgesagt bzw. verschoben und ab in die Werkstatt zum Endspurt. Endlich Kühlwasser auffüllen und den ersten richtigen Probelauf durchziehen.
Ich habe mich mittlerweile entschloßen den Messingkühler nicht wieder zurück ins Regal zu legen. Vielleicht hat er ja tatsächlich eine etwas bessere Kühlleistung.
Also die ganzen Kühlerpappen und den Thermoschalter vom alten Kühler umgebaut. Das Lüfterblech mit dem Lüftermotor und dem Gummilappen bestückt und dann beides zusammengeschraubt.
Dann die ganze Einheit ins Fahrzeug. Unten festgeschraubt, Thermoschalter angeschloßen und unteren Kühlerschlauch ran.
Oben und seitlich befestigt, oberen Kühlerschlauch ran und ab zu Teil 1 der Überschrift: Wasser marsch!
Jetzt stand dem ersten längeren Testlauf nur noch der Stecker des Lüftermotors im Weg. Der alte Kabelbaum und der stärke Lüftermotor wollten nicht so recht zueinander passen.
Ich hatte jetzt aber keine Lust mehr nach einem passenden Stecker zu suchen und habe die Kabelschuhe aus dem Steckgehäuse herausgeholt und sie erstmal so am Motor angeschloßen.
Jetzt wurde es Zeit für Teil 2 der Überschrift: Feuer frei!
Zunächst zickte er noch ein bisschen. Er ging immer wieder aus und ich mußte den Motor zunächst mit kleinen Gastößen am Leben halten. Wie schon vermutet, habe ich bei dem ganzen Gewurschtelt rund um dem Öldruckgeber, den Verteiler wohl etwas verdreht. Nach einer kleinen Korrektur gings dann aber los.
Noch einmal kurz die Zündung abgeblitzt, den Luftfilterdeckel rauf und dann hieß es: Prost!
Zur Feier des Tages habe ich mir ausnahmsweise wirklich mal ein Bierchen gegönnt. Kommt ja selten vor, aber gestern war mir einfach danach. Verständlich, oder?
Einen kleinen Wehrmutstropfen hatte ich dann aber doch noch zu verzeichen: Vorne an der Kopfdichtung hingen ein paar Öltropfen….
Allerdings entpuppte sich die Sache als nicht ganz so tragisch wie zunächst vermutet. Wie auf dem Bild, konnte man es auch in natura zunächst nur sehr schwer Eingrenzen. Das frische Öl erschwerte die Sache. Es kommt aber von weiter oben. Entweder der Nockenwellensimmering oder die Ventildeckeldichtung, die ich noch nicht erneuert hatte, sind schuld.
Wenn das alles ist, kann ich darüber nur lächeln. Daß bei so einem umfangreichen Projekt, irgendwo etwas nachgearbeitet werden muß, hatte ich eingeplant.
Das konnte mir den Tag aber natürlich in keinster Weise vermiesen.
Wenn er Strom und Sprit hätte, würde er laufen!
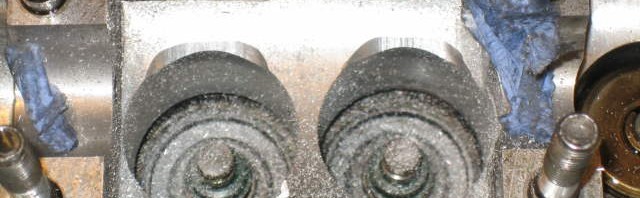
Endlich kann ich einen Schlußstrich unter das Kapitel Nockenwelle machen. Die Welle ist drin, die Plättchen bleiben liegen und drehen tut sie sich auch.
Bevor es gestern allerdings soweit war, mußte ich noch ein wenig mit dem Dremel hantieren.
Was eine Sauerei. Mir wäre wohler gewesen, wenn der Kopf noch auf der Werkbank liegen würde. Die Ölbohrungen habe ich alle mit Putzlappen verschlossen. Man beachte den gelben Lappen oben links auf dem Bild. Der wird am Ende des Artikles noch eine ganz besondere Rolle spielen.
Ich war so vertieft in die Arbeit, daß ich erst wieder ein Foto gemacht habe, als die ganze Späne weggeblasen und die Ventile schon wieder montiert waren.
Jetzt ist ausreichend Platz zwischen Nocken und Kopf vorhanden. Zeit mal den Riemen auf die Orgel zu legen. Ich brauchte endlich mal wieder einen Anblick an dem ich mich berauschen konnte.
Den Motor habe ich dann mehrfach durchgedreht. Nach soviel Stolpersteinen ein wahrlich geiles Erlebnis. Endlich am Ziel.
Warum ich ohne verstellbares Nockenwellenrad keine vernüftige Steuerzeiteneinstellung hinbekomme, sieht man hier.
Die waagerechte Markierung an der Stirnseite der Nockenwelle fluchtet genau mit der Kopfoberkante und das Nockenwellenrad muß fast einen halben Zahn ausgleichen. Der Riemen kommt aber noch mal wieder runter. Ich muß noch die Ventile einstellen und der Simmering für die Nockenwelle ist auch noch nicht wieder drin.
Zum Schluß wie versprochen noch mal etwas zu den gelben Putzlappen vom ersten Foto. Den habe ich nämlich beim Ausblasen des Kopfes mal eben locker in der Bohrung versenkt. Weg war er, irgendwo in den Tiefen des Motors verschwunden. Mir war das zunächst egal. Gestern war die Nockenwelle dran und davon ließ ich mich auch nicht abbringen.
Ich war schon wieder umgezogen und hatte die Suche nach dem Lappen eigentlich schon auf einen der folgenden Tage verschoben, da packte mich doch noch der Ehrgeiz. Bewaffnet mit einer Taschenlampe machte ich mich auf die Suche. Nichts zu finden. Also noch mal die Luftpistole in sämtliche Öffnungen reingehalten, damit das Stück sicher in der Ölwanne liegt. Den Motor noch ein paar Mal auf dem Motorständer in alle Richtungen gedreht, bis ich mir sicher war: Er muß jetzt in der Ölwanne liegen!
Und tatsächlich. Nach nur wenigen Versuchen, ihn mit einem Greifer durch die Ölablaßbohrungen zu erwischen, hatte ich ihn am Haken.
Es gibt halt auch Tage, an denen gelingt einfach alles. Zum Glück.
Raus, rein, raus und aus!
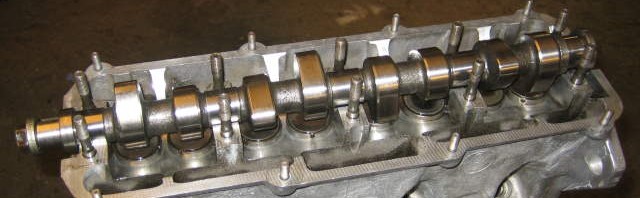
Natürlich gings gestern mit neuem Elan ans Werk. Bewaffnet mit der neuen Nockenwelle gings in die Werkstatt. So schnell hatte ich wohl noch nie eine Nockenwelle umgebaut. 😉
Alte Welle raus, neue Welle rein.
Schnell noch die Schraube zum Durchdrehen rein, Schlüßel rauf und ab gings. Aber nur kurz…
Schon nach kurzer Zeit war Schluß. Es ist genau das eingetreten, was ich gestern schon befürchtet hatte. Die Nocken sind tatsächlich zu hoch. Da dreht sich nichts mehr.
Also die Welle wieder raus, Stößel raus, Druckluft auf den Zylinder und die Ventilfedern wieder aus dem Kopf geholt.
Den Schritt hätte zum Tausch der Ventilfedern zwar eh noch machen müssen, vorher hätte ich aber eigentlich gerne gewußt haben, ob das mit den Einstellplättchen jetzt hinhaut.
Um nicht die ganze Zeit mit dem angeschloßenen Druckluftschlauch arbeiten zu müssen, habe ich den Motor so hingedreht, daß der Kolben ganz oben steht. Die Ventile dann auf den Kolbenboden heruntergedrückt und den Motor weitergedreht bis die Nut im Ventilschaft eben über der Ventilschaftdichtung stand.
Die Ölrücklaufbohrungen im Kopf habe ich schon mal mit ein paar Lappen verschloßen. Jetzt hätte es mit dem Bearbeiten der Kante eigentlich losgehen können. Aber leider hatte ich nichts in der Werkstatt was sich dafür geeignet hätte. Alle Schleif- und Fräsaufsätze lagen von der Krümmer und Kopfbearbeitung noch zu Hause in der Garage.
Ich habe den Motor dann noch schlafen gelegt, damit das Öl abtropfen kann und bin dann nach Hause.
Gute Nacht!
Ventilspiel war´s nicht! – Problem besteht weiterhin
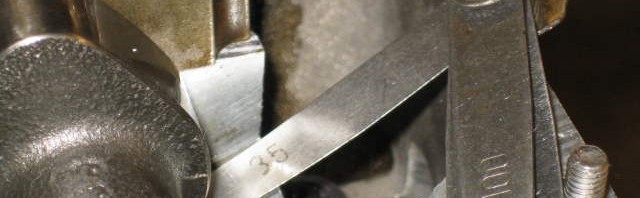
So richtig dran geglaubt habe ich nach Abwägung diverser Fakten schon selber nicht mehr. Es sollte sich dann auch nicht als die Lösung des Problems herausstellen.
Das Ventilspiel habe ich trotzdem mal nach Schrick-Vorgaben eingestellt: 0,35mm Einlaß und 0,45mm Auslaß.
Einer der Gründe warum ich im Vorwege trotzdem nicht so recht daran glauben wollte liegt eigentlich auf der Hand: Nur weil das Ventilspiel nicht 100%ig stimmt, darf es nach meiner Meining nach, nicht zu einem solchen Zustand kommen. Ventilspiel um 2/10 daneben und der Motor geht den Bach runter. Das konnte ich mir nicht mehr wirklich vorstellen.
Trotzdem probiert man ja alles aus, wenn man im Dunkeln tappt. So habe ich es dann auch noch mit der dünnsten aller Einstellscheiben versucht. Die mißt genau 3mm und das Ventilspiel betrug damit über 1mm. Kein Veränderung.
Auch der Versuch mit Null Ventilspiel ergab keinerlei Veränderung.
Hier mit einer nagelneuen 4,05mm Scheibe. Kein Ventilspiel mehr, aber das Plättchen kippt genauso wie vorher.
Mit einige Leuten habe ich das Thema gestern auch schon erörtert, so richtig weitergekommen bin ich aber noch nicht. Ich vermute, daß es sich eventuell doch um eine Nockenwelle für Motoren mit Hydrostößeln handelt. Was mich eben nur stutzig macht, ist die Tatsache, daß die 4.Lagerstelle vorhanden und auch vollkommen ausgearbeitet ist. Bei VW-Wellen ist diese Lagerstelle nicht auf Maß geschliffen und auch der Grundkreis der Nocken ist ein völlig anderer.
Es bleibt spannend.
Um trotzdem nicht nach Hause zu fahren ohne etwas produktives geleistet zu haben, mußte aus Frust die Ölwanne dran glauben.
Ich glaube zum ersten Mal in meiner Schrauberkarierre habe ich die Dichtung mal mit Dichtmittel angesetzt. Ich hoffe ich werde es nicht bereuen. Oder der Vertreter von Normfest, der mir das empfohlen hat und das Dichtmittel in den siebten Himmel gelobt hat. 😉
Nun kleckert mir wenigstens nicht mehr das ganze Motoröl auf den Boden wenn ich mit der Nockenwelle rumexperimentiere. Die Ölablaßschraube fehlt noch, aber dazu gibt es die Tage noch eine kleine Extrastory.
Der Zahnriemen darf jetzt nicht mehr reißen.
Diese Festellung habe ich gestern gemacht, nachdem ich den Kopf montiert hatte. Vorbei die Zeit, daß dieser Motor ein Freiläufer ist. Sollte jetzt ein Zahnriemnriß eintreten, hat das schwerwiegende Folgen.
Aber der Reihe nach. Als erstes habe ich noch mal die alte Kopfdichtung mir der neuen, die eigentlich für den 1,5l-Diesel vorgesehen ist, verglichen. Bis auf teilweise ein wenig anders ausgeführte Durchbrüche für die Kühlwasserkanäle paßt sie einwandfrei.
Mittels zweier abgesägter und mit ein Schlitz versehenen Zylinderkopfschrauben habe ich sie dann auf dem Block positioniert.
Durch die Schrauben hatte ich auch gleich ein Führung zum Aufsetzten des Kopfes. Kopf rauf, Kopfschrauben angezogen. Kein großes Thema. (mehr …)
Ventile eingeschliffen und montiert
Langsam fügt sich das Puzzel wieder zusammen. Gestern gings los mit dem Zusammenbau des Zylinderkopfes. Erster Schritt war das Einschleifen der Ventile.
Ein Arbeit die ganz schön Zeit kostet. Ich mußte immer wieder mal eine kleine Pause einlegen, weil mein Arm vom Kurbeln lahm war. Einen Durchgang habe ich mal im Video festgehalten. (mehr …)